The Latest from Kansas Farmer
Steve and Cindi Ohlde surrounded by family at K-State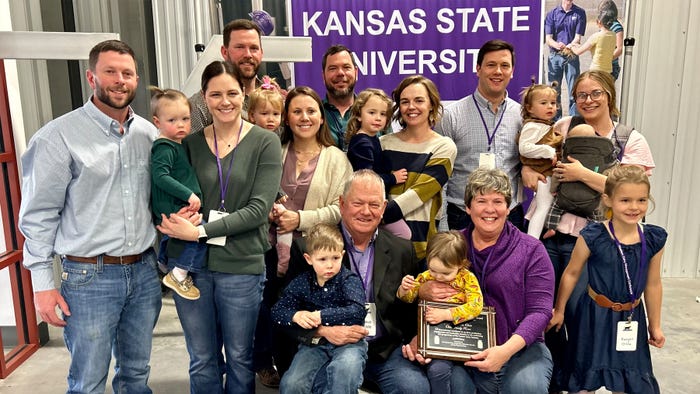
Dairy Cattle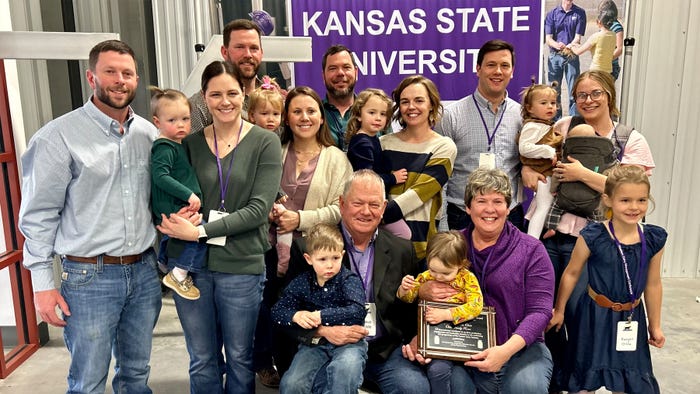
Ohldes expand family dairy legacyOhldes expand family dairy legacy
Steve and Cindi Ohlde of Ohlde Family Farms named the 2024 Kansas Distinguished Dairy Family.
Market Overview
Contract | Last | Change | High | Low | Open | Last Trade |
---|---|---|---|---|---|---|
Jul 24 Corn | 452.5 | +0.5 | 453 | 451.5 | 451.75 | 07:53 AM |
Jul 24 Oats | 355.25 | +4.25 | 356.75 | 352.25 | 352.25 | 07:39 AM |
May 24 Class III Milk | 18.25 | +0.07 | 18.28 | 18.25 | 18.28 | 04:21 AM |
Jul 24 Soybean | 1178.25 | -1.5 | 1181 | 1178 | 1179 | 07:53 AM |
Aug 24 Feeder Cattle | 258.3 | +2 | 258.8 | 254.25 | 256.425 | 06:04 PM |
May 24 Ethanol Futures | 2.161 | unch — | 2.161 | 2.161 | 2.161 | 09:38 PM |

Copyright © 2019. All market data is provided by Barchart Solutions.
Futures: at least 10 minute delayed. Information is provided ‘as is’ and solely for informational purposes, not for trading purposes or advice.
To see all exchange delays and terms of use, please see disclaimer.
All Kansas Farmer
Subscribe to receive top agriculture news
Be informed daily with these free e-newsletters